Inhalt dieses Artikels
Wir heißen Sie auf unserem neuen Blog herzlich willkommen!
Ab sofort berichten wir hier regelmäßig über spannende Neuigkeiten, erklären technische Fachbegriffe leicht verständlich und widmen uns interessanten Themen aus dem Bereich des Engineerings sowie aus der gesamten weiten Welt der Kunststofftechnik.
Starten möchten wir mit dem Insert-Spritzguss. Hier handelt es sich um ein Verfahren, welches von uns – natürlich nach höchsten Standards – sehr häufig eingesetzt wird und Ihnen wesentliche Vorteile bietet. Welche das sind, erläutern wir im Laufe dieses Artikels.
Das Umspritzen von Einlegeteilen – was alles möglich ist
Der Begriff „Insert“ stammt aus dem Englischen und bedeutet „Einlage“. Und genau darum geht es beim Insert-Spritzgießen / der Inserttechnik: Ein Einlegeteil wird in eine Form beziehungsweise ein Werkzeug eingebettet und dann mit Kunststoff umspritzt.
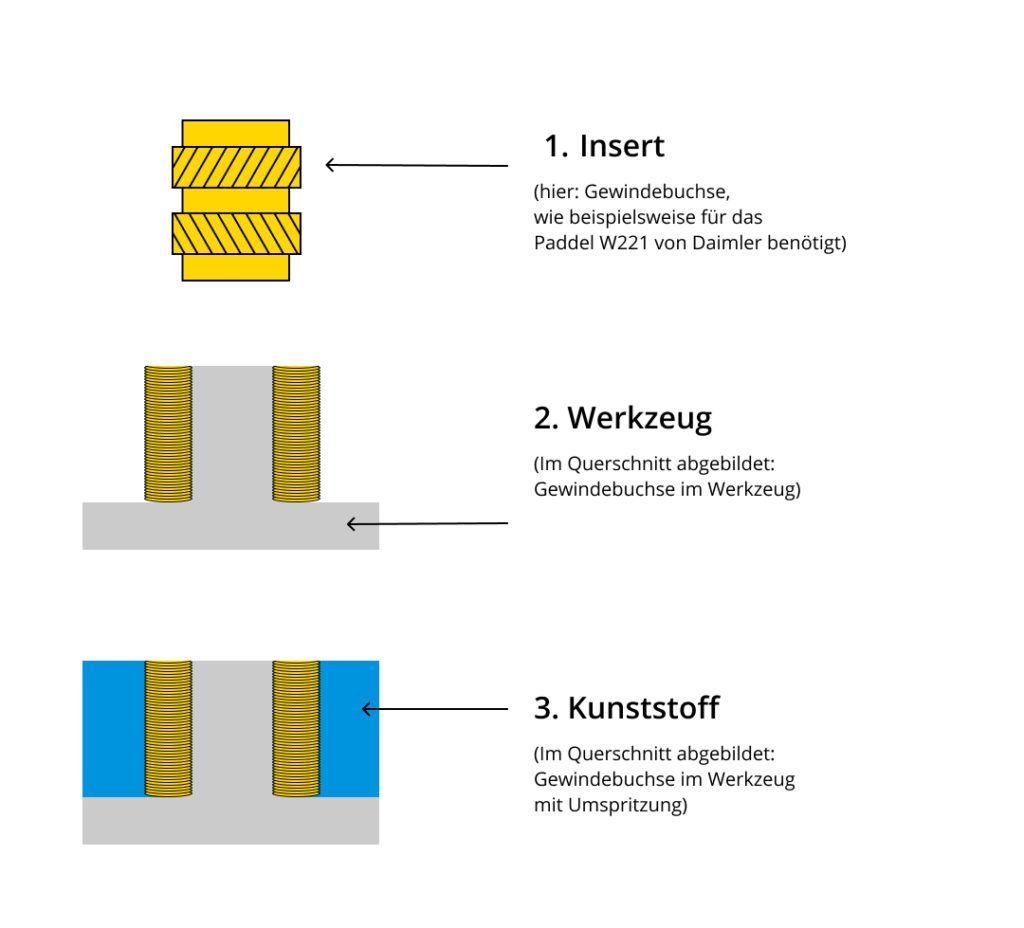
Schauen wir uns das Umspritzen von Einlegeteilen näher an. Vorrangig lassen unsere Kunden Funktions- oder Formteile wie Metallstifte, Gewindeeinsätze, Muttern, Lagerbuchsen, Griffe für Schraubendreher oder Griffe für Messer umspritzen. Der Insert-Spritzguss ist aber nicht nur zum Umspritzen von Metall-Einlegeteilen geeignet, sondern auch zum Umspritzen elektrischer Kontakte, von Achsen, von Siebeinfassungen oder von multifunktionalen Bauteilen, die sonst nicht anders herzustellen sind.
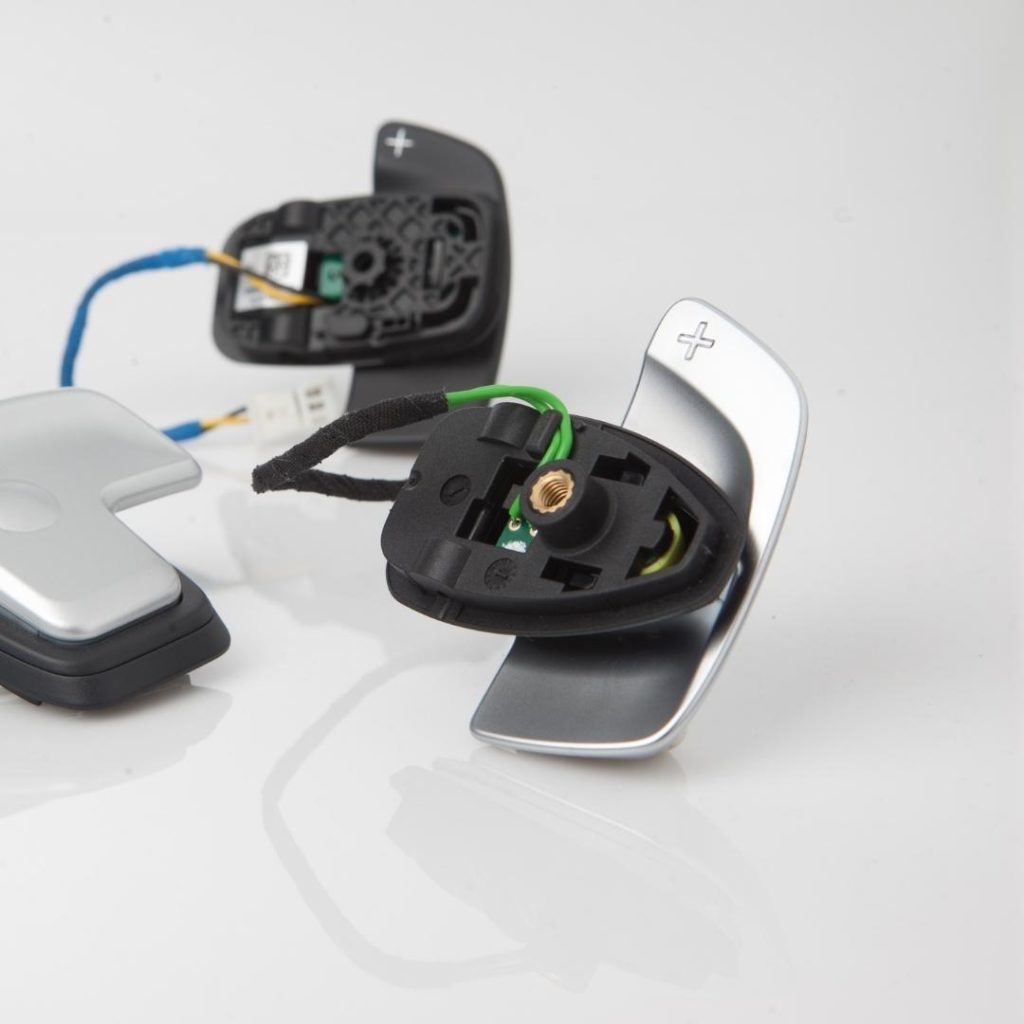
Auch gänzlich andere Materialien lassen sich mit einer sinnvoll gewählten und geeigneten Kunststoff-Formmasse umspritzen beziehungsweise kombinieren – wie beispielsweise Duromere (Duroplaste) oder Elastomere. Bei letzterem handelt es sich um formfeste, aber elastisch verformbare Kunststoffe. Auch Glas-, Keramik- oder Hightech-Kunststoffeinlegeteile lassen sich umspritzen. Beim Schaffen von hybriden Strukturen ist generell ein großer Spielraum möglich.
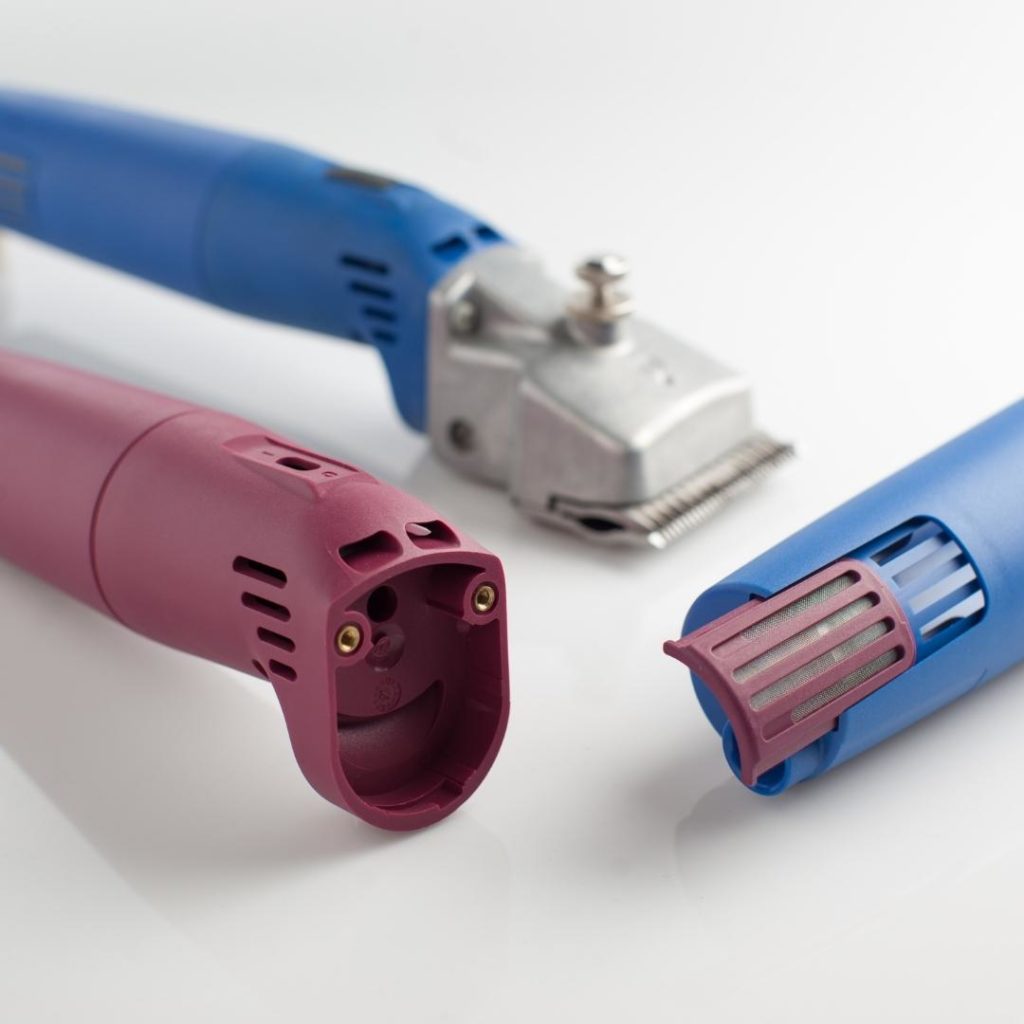
Dabei ist es möglich, die Inserts vollständig oder nur teilweise zu umspritzen. Gerade bei Einlegeteilen wie Gewindeeinsätzen, die die mechanischen Eigenschaften von Kunststoffteilen stärken sollen, wird oft ein einseitig gerichtetes Umspritzen verwendet. Dies ist vor allem bei Endprodukten, die wiederholt montiert werden, von Vorteil.
Inserttechnik vs. Outserttechnik – zwei Verfahren im Hybridspritzguss
Im Gegensatz zu der Outserttechnik, in dem Metall gegenüber dem Kunststoff vom Volumen her überwiegt, ist bei der Inserttechnik das Gegenteil der Fall: hier überwiegt der Kunststoff gegenüber dem Metall im Volumen. Beide Techniken stellen Hybridtechniken dar und gehören somit zur Technik des Hybridspritzgusses. Neben dem Insert-Spritzguss gibt es noch weitere Verfahren, welche sich in der Herstellung von Hybridstrukturen etabliert haben – wie zum Beispiel das Verkleben, das Schweißen, die Montage oder die Coextrusion („Stranggießen“) von Einlegeteilen.
Die Wahl des idealen Werkzeugs im Insert-Spritzguss
Bei der Konstruktion des für den Insert-Spritzguss passenden Werkzeugs ermitteln wir den optimalen Anspritzpunkt per Füllsimulation; so lässt sich das Füllverhalten nicht nur vorhersehen, sondern auch deutlich verbessern. Für den Werkzeugbau stehen uns verschiedene Simulationsmethoden zur Verfügung. Unsere Software berechnet dabei sämtliche wichtigen Parameter, die es zu berücksichtigen gilt – wie zum Beispiel die Druckverteilung, die Temperaturen oder die Schließkraft.
Arten der Zuführung: Vollautomatisches Einlegen oder Einlegen per Hand
Das Einlegen des Inserts im Fertigungsprozess erfolgt dann entweder händisch oder vollautomatisch – was häufig abhängig von der benötigten Stückzahl ist. Von ihr hängt auch wiederum die Art und Weise der vollautomatischen Zuführung ab. Auch die Produktgeometrie selbst gehört zu den weiteren Faktoren, die die Zuführungsart beeinflussen und bestimmen.
Eine vollautomatische Zuführung kann über Wendelförderer bzw. Schwingförderer erfolgen. Darüber hinaus kann die Bestückung auch über 6-Achs-Roboter, wie beispielsweise von Kuka, vorgenommen werden. Da diese Roboter frei programmierbar sind, lassen sie sich sehr flexibel einsetzen. Aber auch der Einsatz von speziellen Handlingsgreifern ist möglich. Gerade wenn die Zuführung immer gleich erfolgt, lassen sich solche Handlingsgreifer ideal auf einen spezifischen Anwendungsfall konzipieren.
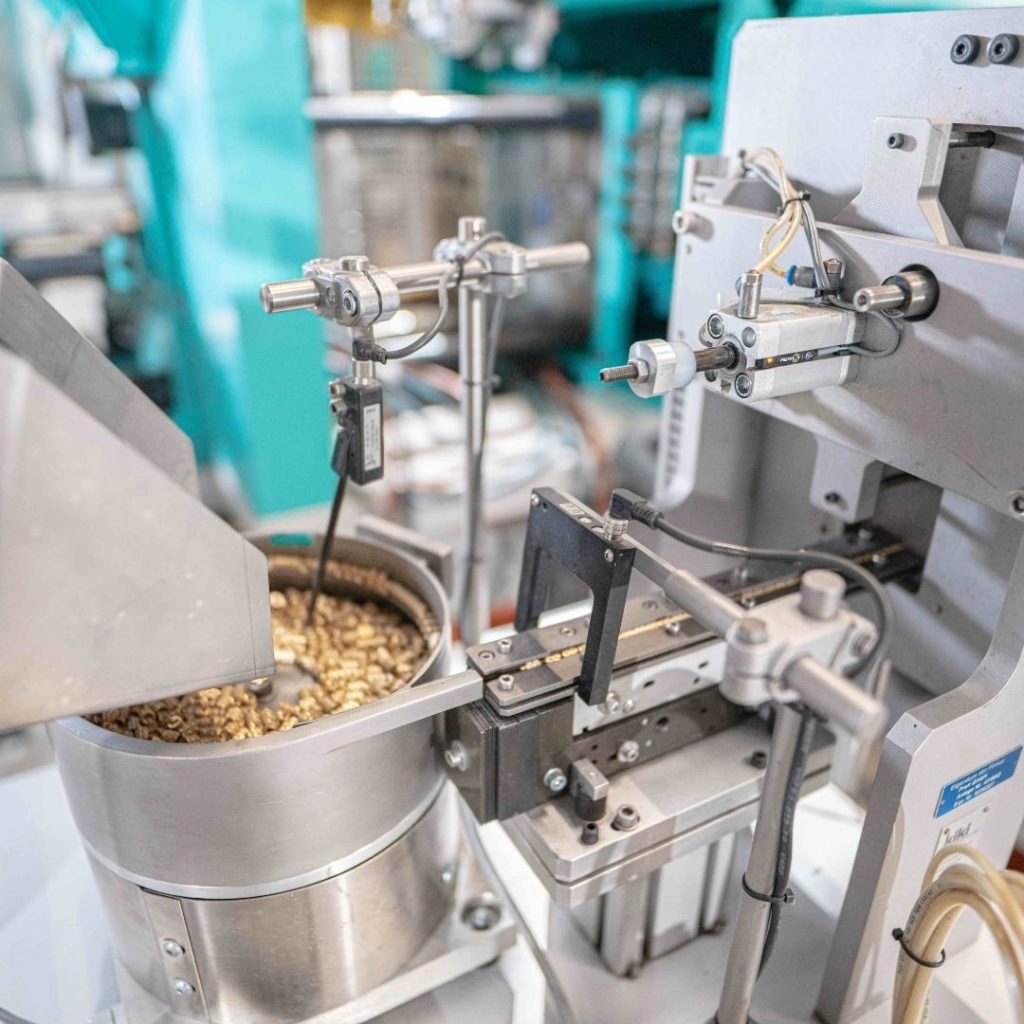
Sogenannte Linearförderer eignen sich hervorragend, wenn wenig Platz gegeben ist. Auch schwere Masseteile können mit ihrer Hilfe befördert werden. Bei leichtgewichtigen Masseteilen wiederum kommen oft Zentrifugalförderer zum Einsatz, die teileschonend sind und an der Spitze der Hochgeschwindigkeitszuführung stehen. Daneben kommen beispielsweise auch Stufen- oder Flächenförderer zum Einsatz. Ist eine manuelle Bestückung vorgesehen, wird das Insert von einem Maschinenbediener eingelegt.
Um im Umspritzzyklus viel Zeit zu sparen, kommen bei uns vorzugsweise Vertikalmaschinen mit Schiebe- oder Drehtisch zum Einsatz. Während der Spritzphase können Roboter sowohl ein Insert einlegen als auch ein fertiges Teil entnehmen.
Ausgeklügelte Kamerasysteme im Fertigungsprozess
Je nach Anforderungen und Stückzahlen kann dieser Fertigungsschritt auch sehr gut mit entsprechenden Kamerasystemen kombiniert werden. Dadurch lässt sich sowohl eine 100 % Kontrolle der Inserts als auch der fertigen Kunststoffteile realisieren. Die Inserts sollten idealerweise vorgewärmt und „metallisch blank“ (gereinigt und unbeschichtet) eingelegt werden. Um ein Überspritzen der Inserts zu vermeiden, sind kunststoffgerechte Toleranzen im Bereich der Dichtflächen erforderlich.
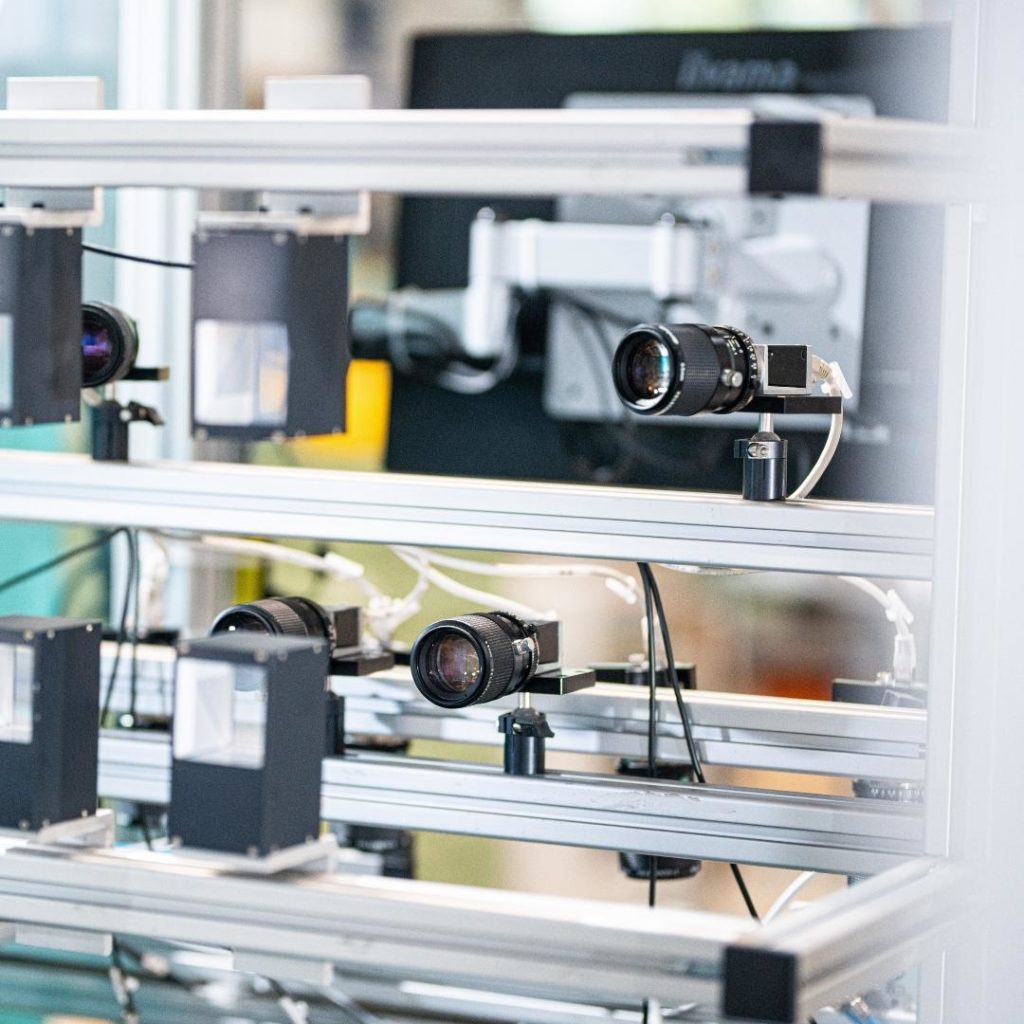
Sicherer Halt für Ihr Einlegeteil im Insert-Spritzguss
Kann das Halten des einzulegenden Teiles durch reines Einlegen in das Werkzeug nicht gewährleistet werden, lässt sich durch Stützstifte, Magnete, Schnappeinrichtungen oder ein angelegtes Vakuum eine sichere Lage erreichen. Genauso wichtig ist in diesem Zusammenhang eine möglichst sinnvolle Schmelzeführung zu wählen, da der in der Kavität, also der in der Aushöhlung entstehende Werkzeuginnendruck einen Einleger entweder in der gewünschten Position halten oder aber abheben und verschieben kann.
Die Vorteile der Inserttechnik liegen auf der Hand
1. Ersparnis in mehrfacher Hinsicht:
Dank des Wegfalls zusätzlicher oder nachträglicher Montage-Schritte werden Zeit, Energie und Kosten gespart.
2. Eine effizientere Produktion:
Durch das Umspritzen entfallen zusätzliche Bauteile, was wiederum vor allem Größe und Gewicht des Endprodukts reduziert.
3. Stabilisierung schaffen:
Es werden mechanisch feste Verbindungen geschaffen, die eine verbesserte Beständigkeit und Abriebfestigkeit aufweisen können.
4. Ein Zugewinn an Ästhetik und Design:
Das Endprodukt zeigt nicht nur höchst funktionale Eigenschaften auf, sondern kann auch in Form, Haptik und Optik optimiert werden. Zusätzlich stehen Ihnen hier auch verschiedene Möglichkeiten der Oberflächenveredelung zur Verfügung.
5. Generelle Verbesserung der Produkteigenschaften:
Sowohl die funktionellen als auch die mechanischen Eigenschaften des Kunststoffteils lassen sich zum Teil signifikant verbessern. Sogar das Herstellen einer thermischen oder elektrischen Isolierung ist möglich.
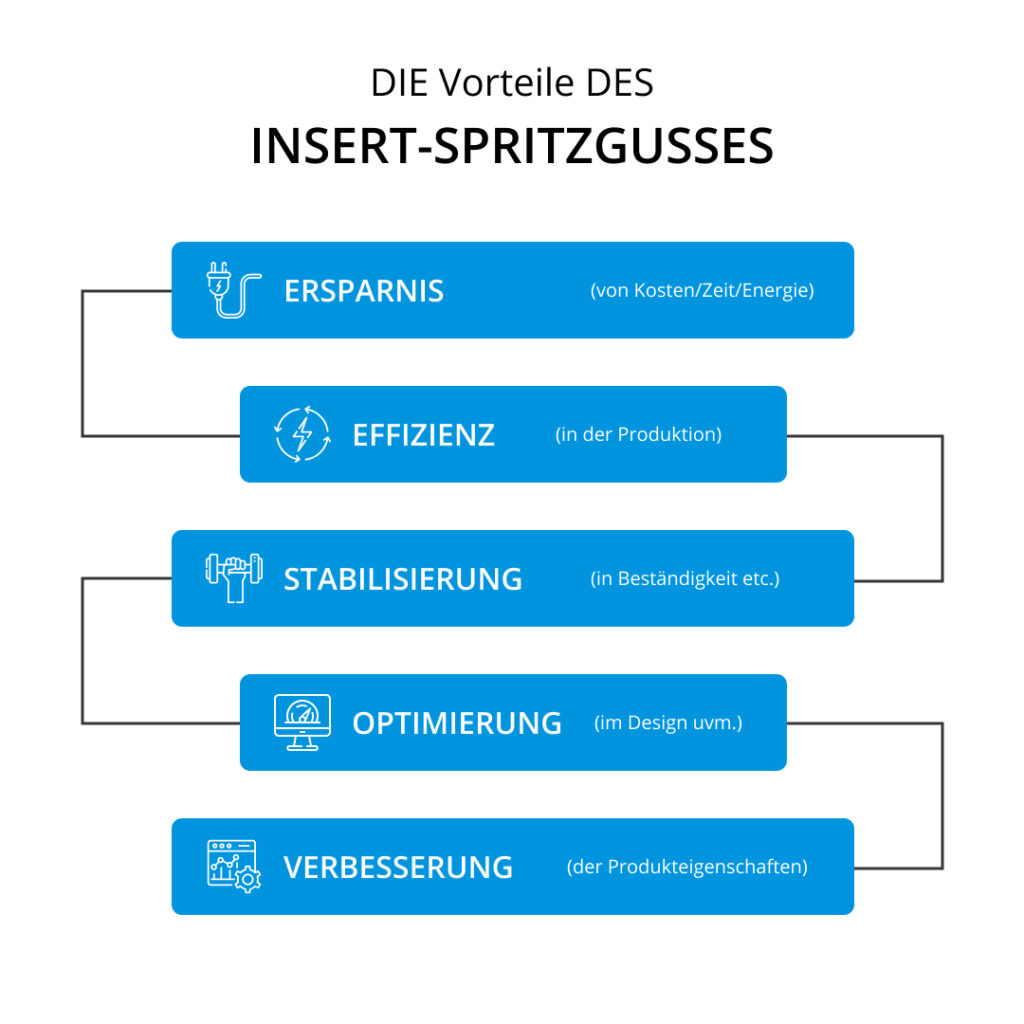
Zu beachten ist bei Punkt 5, dass mechanisch hochfeste Bauteile nur bedingt realisierbar sind. Empfehlenswert ist an dieser Stelle immer auf ein entsprechendes Lastenheft zu bestehen, in dem die Anforderungen (wie beispielsweise Belastungsfälle), die chemische Beständigkeit, die Optik und die Haptik eindeutig definiert und festgehalten sind. Des Weiteren ist im Vorfeld eine Auszugskraft zu definieren.
So, nun sind wir bereits am Ende unseres allerersten Blog-Artikels angelangt.
Sie sind neugierig geworden, wie solch ein Herstellungsprozess im Insert-Spritzguss ablaufen kann? Hier gehts zum Video!
Sie haben Fragen oder Anregungen? Nehmen Sie gerne Kontakt zu uns auf – wir freuen uns!